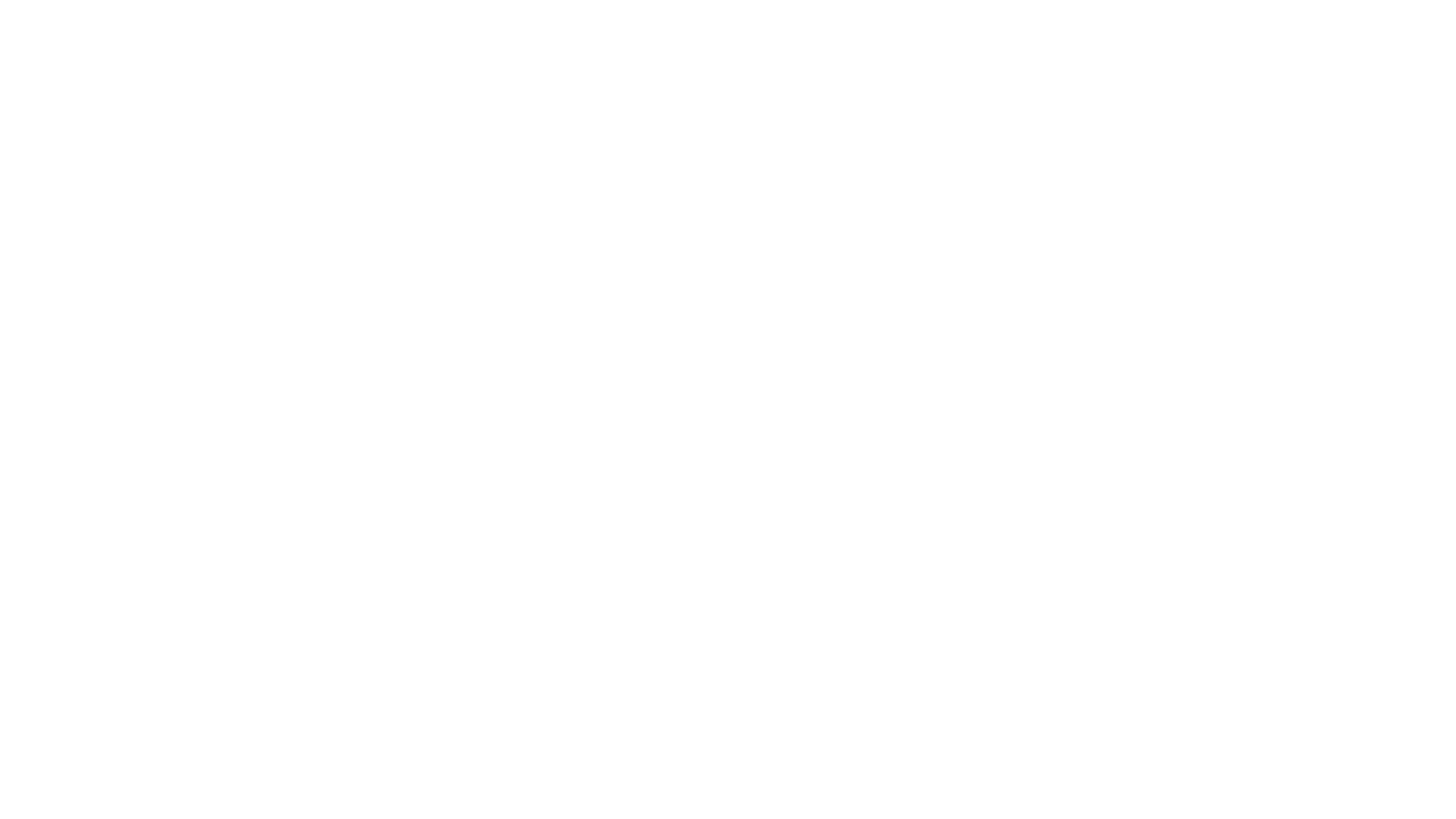
Why Challenge Handmade Tires? (#)
Challenge Handmade Tires combine attributes to create the most comfortable and low rolling resistance tires:
- Soft, supple casings
- Soft natural rubber treads with special compound
- Unique, seamless latex inner tubes
- Special puncture protections
Sidewall sealants
Challenge Handmade Tubulars (H-TU) and Handmade Clinchers (H-CL) (#)
We make Challenge Handmade Tires 100% in our family-owned factory in Thailand, 90 minutes down the coast from Bangkok. We are in Thailand because that is where our natural rubber and latex is sourced, where we can control the raw materials and where the world’s rubber and latex experts work.
Challenge Handmade Tubulars (H-TU) (#)
Our Handmade Tubular (H-TU) tires perform better than any tubeless system! This is why they are raced by all of the top athletes and teams in every cycling segment.
The latex inner tube us cradled inside the high quality casing that is sewn shut, forming a soft protective layer for the delicate tube. A
base tape is glued over the sewing for protection and to absorb the adhesive later applied to hold the tubular on the rim. The carcass is mounted on a rim, inflated and a special natural ru
bber tread is precisely glued on top. Puncture protection layers and sealants can be applied to the finished casing, depending on the tubular’s use.
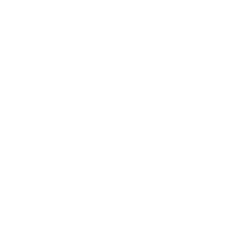
Tubular vs. Clincher
Handmade TLR (H-TLR) and Handmade Clincher (H-CL) (#)
New Handmade TLR (H-TLR) and Handmade Clincher (H-CL) tires perform better than any vulcanized tubeless system! Challenge Handmade TLR and H-CL are made from the same materials and processes as our handmade tubulars but instead of sewing an inner tube inside the casing is wrapped around a aramid bead to form a tire that fits on a clincher rim.
The HTLR is molded flat, not in a horseshoe like a V-TLR or V-CL. This shape allows the casing to naturally deform over surface imperfections and minimize rolling resistance. A normal vulcanized tubeless tire is molded in a U-shape to make the sidewalls rigid so the system does not “burp” or lose air when it deforms after it encounters a surface imperfection. The new Challenge H-TLR is anything but normal. Where V-TLR is stiff, high rolling resistance and uncomfortable to ride, the new H-TLR maintains the soft supple qualities of all Challenge Handmade tires but sets up with a sealant on TLR wheels.
A bead-to-bead inner coating gives added puncture protection to these new H-TLR tires and greatly reduces any air pressure dissipation. Enhanced longevity has been gained with the addition of an aramid bead protection strip, to reduce rim chafing. The proven Challenge road products, (Strada, Paris-Roubaix and Strada Bianca), all with herringbone treads are available in H-TLR with some of the lowest weights in the market.
The popular Gravel treads (Strada Bianca, Almanzo and Gravel Grinder) are also released in H-TLR with the same competitive weights for gravel tires. The unique Challenge Handmade Tubeless system is the closest thing to a high performance Handmade Tubular that you can fit on a tubeless Ready clinchers
Handmade Clincher/ Tubeless ready vs. Vulcanized Clincher
Handmade Tubeless Tubular (H-TLTU) (#)
All Challenge Gravel treads now offer this unique H-TLTU system that maintains all the performance benefits of the best handmade tubulars. A latex liner is fused to the casing, replacing the traditional inner tube, allowing for the use of a plug to finish a ride or race in case of a puncture too large for the sealant to fix.
Tire Construction Basics (#)
To understand what makes Challenge Handmade tire construction special you must first understand the basics of bicycle tire construction. 98% of the world’s bicycle tires are wire bead clinchers made with a nylon casing saturated with synthetic butyl rubber and a synthetic butyl rubber tread. Those components are cooked or vulcanized into a horseshoe or U-shaped circle to be mounted on a steel or alloy or carbon clincher rim.
This system maximizes the durability and long life and minimizes the cost of the tire. Car tires, motorcycle tires, airplane tires and giant truck and tractor tires are all made much the same way. Repeat, this is the cheapest, most cost efficient way to make a tire.
Butyl Rubber (#)
Butyl rubber is that material you find in bouncy playground balls, bladders of footballs, basketballs and soccer balls (to make them bounce) and cheap, standard bicycle inner tubes. The main attributes of butyl rubber are its inexpensive price and ability to bounce.
Vulcanized Clinchers (V-CL) (#)
To make a standard Vulcanized Clincher (V-CL), nylon mesh is dipped in a bath of butyl rubber and then calendared (squeezed) between big steel rollers to create the casing. Because the thread count is so low, there are big spaces between threads to fill with bouncy butyl rubber. The final casing is about 50-70% nylon and 30-50% butyl rubber (higher thread count, less butyl rubber). The casing is combined with the butyl tread rubber and vulcanized into the clincher shape. VCL is durable but not comfortable or high performance.
Strong, cheap standard nylon/butyl rubber tire systems for cars, trucks, airplanes, tractors and motorcycles may be attractive when you have a sophisticated suspension system and padded seats separating you from road shock. When you have a lightweight, high-performance bicycle where only six or eight kilos of super stiff carbon fiber (wheels, fork, frame, bar, stem, seat post and even saddle shell) highly optimized for efficient power transmission separating you from the road or trail, a bouncy (at low pressure) or stiff (at high pressure) V-CL tire system delivers a painful, exhausting and inefficient ride when it is dry - and a quite dangerous ride when it is wet.
Vulcanized Tubeless Ready (V-TLR) (#)
The highest level of performance offered by car, truck and motorcycle tire manufacturers is a vulcanized tubeless system. While this is an old technology for cars and trucks, for bicycles it is relatively new and did not even have an internationally accepted design standard (ISO or ETRTO) until this year.
By eliminating the inner tube it is possible to lower the weight and theoretically create a softer, more comfortable, more efficient, lower rolling resistance tire system by running lower tire pressure. The reality is a little different as extra rubber needed to seal the air lower pressures tends to defeat the concept of “high performance” tubeless.
A tubeless system has a super tight fit on the rim to maintain the seal and can be run without sealant. Most tubeless tires are actually tubeless ready (TLR), able to run tubeless by adding a sealant but also able to be run with an inner tube when assembled and sold to make test rides and a quick sale possible. Regardless of which tubeless system is used, two concerns arise:
- A tubeless system requires more maintenance than a system with an inner tube. This is not a big problem in a car or truck or motorcycle that you take to a shop for service, but can be a big problem for cyclists out on the road or trail,
- It is still impossible to make a tubeless system perform like a handmade tubular system. This is why top pros in every bicycle segment still use tubulars.
Challenge started introducing Vulcanized Tubeless Ready (V-TR) tires this year because the ISO and ETRTO standards for proper V-TR tire and rim fit have finally been completed. These standards ensure your safety and your ability to fit and service the tires with hand tools.
Road (or Trail) Shock and Rolling Resistance #1 (#)
Understanding how road shocks are propagated through the bike is critical. Rolling down the road or trail it impacts cracks, holes and rocks perpendicular to the tire surface. The force of these impacts is split into two components - vertical and horizontal.
The vertical force is passed up through the wheels, spokes, fork, frame and into the hands, feet and backside of the rider. This force creates pain, fatigue, poor traction and cornering therefore reducing control especially in the wet.
Twenty years ago steel or titanium or alloy forks, frames and components would have absorbed some of these shocks. Now with all these parts made in carbon fiber optimized for efficient power transmission, all the shocks are passed into the rider. For 15 minutes these shocks may be OK but after an hour or more, the cumulative impacts are both painful and fatiguing.
The compliance of a properly inflated tire has been measured to be 20 times greater than the entire rest of a modern carbon bike – bringing back some comfort and control where only pain existed. A soft, supple tire (especially a tubular) will protect the rider keeping the tire on the ground to optimize traction and cornering.
The horizontal force of impacting these bumps pushes the wheel and bike backward, forcing the rider to apply more power. This force is rolling resistance (Crr).
On a polished indoor track with slick tires at high pressure this rolling resistance is quite small but it grows quickly as even small imperfections on an outdoor concrete track, asphalt road or dirt or gravel trail grow. Crr doubles or quadruples on poorly maintained roads full of cracks and potholes, gravel roads and rocky mountain trails.
HANDMADE FEATURES (#)
Silk (Seta) Ultra S Casings (#)
The easy way to think of the three types of handmade casings is similar to shirts of the same material. The finest casings, like the finest suits, ties, scarves and shirts, are made of silk. Silk is a strong, soft, natural fiber material but the extreme expense and difficult construction mean this level of quality is priced almost exclusively for World Championship and Olympic competitions.
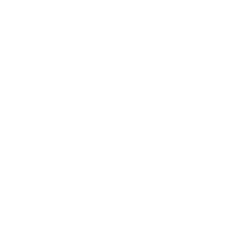
Corespun Cotton SC S and TE S Casings (#)
Corespun cotton casing tires are prepared for our Service Course S (SC S Track, TT, Tri & Road) and Team Edition S (TE S Cross) tires. Cotton is naturally softer and more supple (like your favorite shirt) than an inexpensive polyester shirt and needs to be treated more carefully. Cotton is more likely to absorb water, stain, mold and rot if not properly washed and dried than more durable polyester or more expensive silk. Cotton benefits most from our S Sealant (see below).
Cotton is really the ideal balance of price and performance and therefore is the workhorse casing for professional athletes.
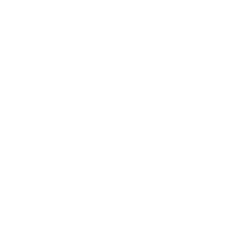
Challenge S Casing Sealant (#)
To protect our new Challenge SC S and TE S cotton and Ultra S silk tires we are now applying a special waterproof bead-to-bead coating in our factory. The new sealant keeps the casings lighter, softer and more supple, eliminating hours of extra effort, keeping the tires looking bright and extending their life.
This new Challenge sealing technology replaces the need to seal by hand with Aquaseal® or Aquasure® or a similar sealant.
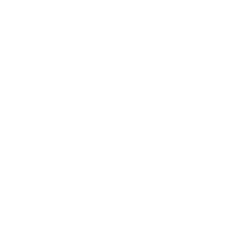
Polyester Pro Casings (#)
Polyester is the least expensive handmade casing. It is a synthetic that is quite strong and impervious to water but not as soft and supple as either cotton or silk. It is far softer and stronger then nylon. We use polyester or SuperPoly (higher tread count polyester) to make our workhorse, more cost efficient Pro level tires.
Our natural rubber treads (#)
Synthetic rubber is cooked and hardened to increase life at the expense of performance, comfort and control. Challenge Handmade natural rubber treads are compounded to add just the right degree of durability without compromising their performance, comfort and control. Our tires may wear out 10 – 20% faster than our competitors but the performance and enjoyment during their lifetime is greatly enhanced which is why they are chosen by so many world class professionals.
PPS and PPS2 (#)
The Puncture Protection System is a special fabric placed between a tire’s tread and casing to increase resistance to punctures. Some tires designed for use on rough roads, cobbles and gravel receive PPS2, an additional layer of PPS between the casing and the inner tube.
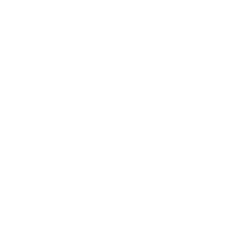
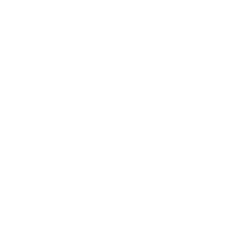
PPS GANZO (#)
Puncture protection strip utilizing flexible, tight weave, multi-component fabric.
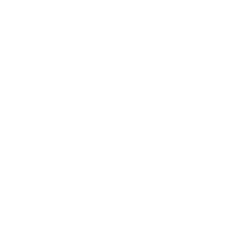
Chafer protection strip (#)
Anti-chafing strip along the casing at the bead. Also acts as a beat-seating aid.
Corazza Armor (#)
Gravel specific casing utilizing double layer 220/260TPI SuperPoly for durability and stability
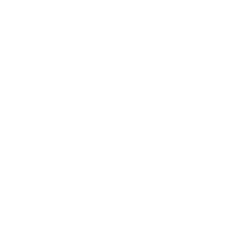
Softer S compound treads (#)
In addition to “S” for the Sealed sidewalls discussed above, some of our tires utilize a softer durometer tread rubber so the “S” also stands for Softer and more Supple. Our segment dominating Team Edition S Cyclocross tires have been fine-tuned by experienced champions and in 2018 they complimented the skills of four World Champions including Sanne Cant, Eli Iserbyt, Evie Richards and Ben Tullet.
The softer “S” treads are also used on the special track tires we have created for British Cycling to support their efforts to steadily improve the performances of their world dominating Track program. Watch for this segment to evolve as more improvements are made during this next Olympic cycle.
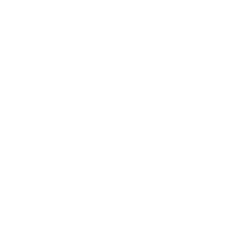
SMARTPlus compound (#)
Gravel specific tread compounds for traction and durability.
Seamless Latex Inner Tube (#)
The final component of the Challenge system is its unique seamless latex inner tube. These tubes are automatically included in all top level Challenge Handmade Tubulars and are the perfect compliment to any clincher but especially Challenge Handmade Clinchers.
Instead of being extruded and joined with an overlap joint like our competitors’ latex tubes, our tubes are seamless meaning they have no joint and therefore no extra weight at that joint or weakness in the system. Our tubes are stronger, lighter, super supple, absorb shock and conform to whatever objects impact it.
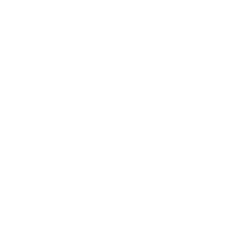
Rolling Resistance #2 (#)
The benefit of all these super supple attributes – treads, casings and latex tubes - is to make our soft and supple Handmade tubulars and clinchers optimally deform over road and trail imperfections – greatly reducing rolling resistance. The latest tests by Tom Anhalt, Josh Poertner, Wheel Energy and Tour Germany show that you save up to 3 watts per wheel just by changing from a butyl to latex inner tube. The rest of our products compliment and protect those soft supple tubes.
In summary, the latex tube compliment our soft casings and treads so that when the tire impacts road and trail imperfections, instead of bouncing, sending shock waves up into the rider, bouncing around corners and forcing an extra burst of energy to overcome the extra rolling resistance, the tire absorbs the bump and rolls over it smoothly, as if it wasn’t there.
Important Note On Handmade Tires (#)
Challenge Handmade Tires are made with the highest quality materials and processes. Like a fine wine, they must stored and treated with care to have a long life and provide the highest level of performance, comfort and control. After being ridden in mud they should be washed with a light detergent with a soft brush and fully dried prior to being stored in cool, dark, dry room (yes, like a wine cellar). Handmade tires should never be stored wet or for long hours in direct sunlight or high heat (on a terrace, in or on a car or in a shop window).
Optimal Operating Pressure (OOP) (#)
The maximum tire pressure is required by international law (the International Standards Organization or ISO) to be marked on the tire. This max pressure has nothing to do with the Optimal Operating Pressure! Max pressure is merely a safe pressure below the pressure where a tire will burst off a correctly designed and built wheel.
The Optimal Operating Pressure (OOP) depends on the course condition, weather condition, rider size and tire size. OOP is critical to minimize rolling resistance while maximizing traction, comfort and control.
If you are riding on an indoor track it is quite easy to find OOP on those 22mm Pista tubulars - just pump them to 12 bar (170psi) and go because rolling resistance is minimal on a polished wood track. As soon as you go outdoors to a concrete track or asphalt road, much less off-road, the situation gets much, much more complicated.
Cyclocross roots ...
The absolute masters of proper tire choice and finding OOP are Belgian cyclocrossers. Every Belgian ‘crosser has their personal mechanic who learned the ideal tubular tread, tire size and OOP for a given course and weather condition and knows that OOP is further fine-tuned on race day. They know how to maximize the tire patch for optimum traction, braking and control while minimizing the risk of pinch-flatting.
Passed on to Gravel and MTB ...
A tiny but growing group of Gravel and Mountain Bike racers understand that the OOP and Tubular system that works in the dirt, mud, snow and ice for Cross also works for them. This is why over the past six years five MTB World Championships, two Olympic gold and a silver medal have been won on Handmade Mountain Bike Tubulars. Even with all the money spent by huge tire manufacturers and sealant producers on R&D and marketing, tubeless systems have not been successful in elite competitions. Tubeless is a dream while Tubulars continue to deliver real results.
Ultimately widely respected on the Road ...
At the same time understanding OOP is spreading globally in Cyclocross, Gravel and MTB, more and more professional road teams are understanding how critical it is to ride handmade tubulars and properly fine-tune tire pressure on the Road. The eighteen World Tour Road teams all have mechanics who keep a table of tire OOP for each rider (by weight), tire volume and course that has been fine-tuned over many years of competitions and this OOP system is spreading as the secret gets out.
More top Road teams know the OOP equation changes from Strada Bianca to Paris-Roubaix to Tour of Flanders to concrete or asphalt, unserviced by years of recession or paved yesterday for the Tour de France. They know OOP needs to be adjusted for the rain and even more if it is the first rain after weeks or months of dry when oil, gas and exhaust accumulate where traffic is high and roads become slick as ice. When the tire patch is optimally adjusted to keep the soft, supple rubber on the road as much of the time as possible (especially in those corners deformed by heavy vehicles braking), riders can relax, focus and perform there best.
Challenge Handmade Tires with OOP deliver ...
Now, with the help of Challenge Handmade Tires you can better understand what the world’s top professional riders, teams and mechanics in every segment - from Track to TT to Road to Cyclocross to Gravel to MTB - have known for years: how the very finest handmade tubulars and clincher tires and tubes can be properly used to provide you with the most comfortable, controllable, highest performance riding you can imagine (and enjoy!).